
After completing the first step, companies are more effective at quantifying the effects of process improvements. A facility can more easily identify opportunities to improve if facility managers know the current efficiency levels. To ensure efficient production, a facility must first have a reliable baseline data set. The company later identified the inefficiencies of the old processes after realizing the time and effort saved by transitioning to a mobile-friendly CMMS. Sure, the job was being done, but not with the same level of information that a modern CMMS could provide. Take the case of Rug Pros, a carpet cleaning company that used to manage their workflow with Excel sheets.
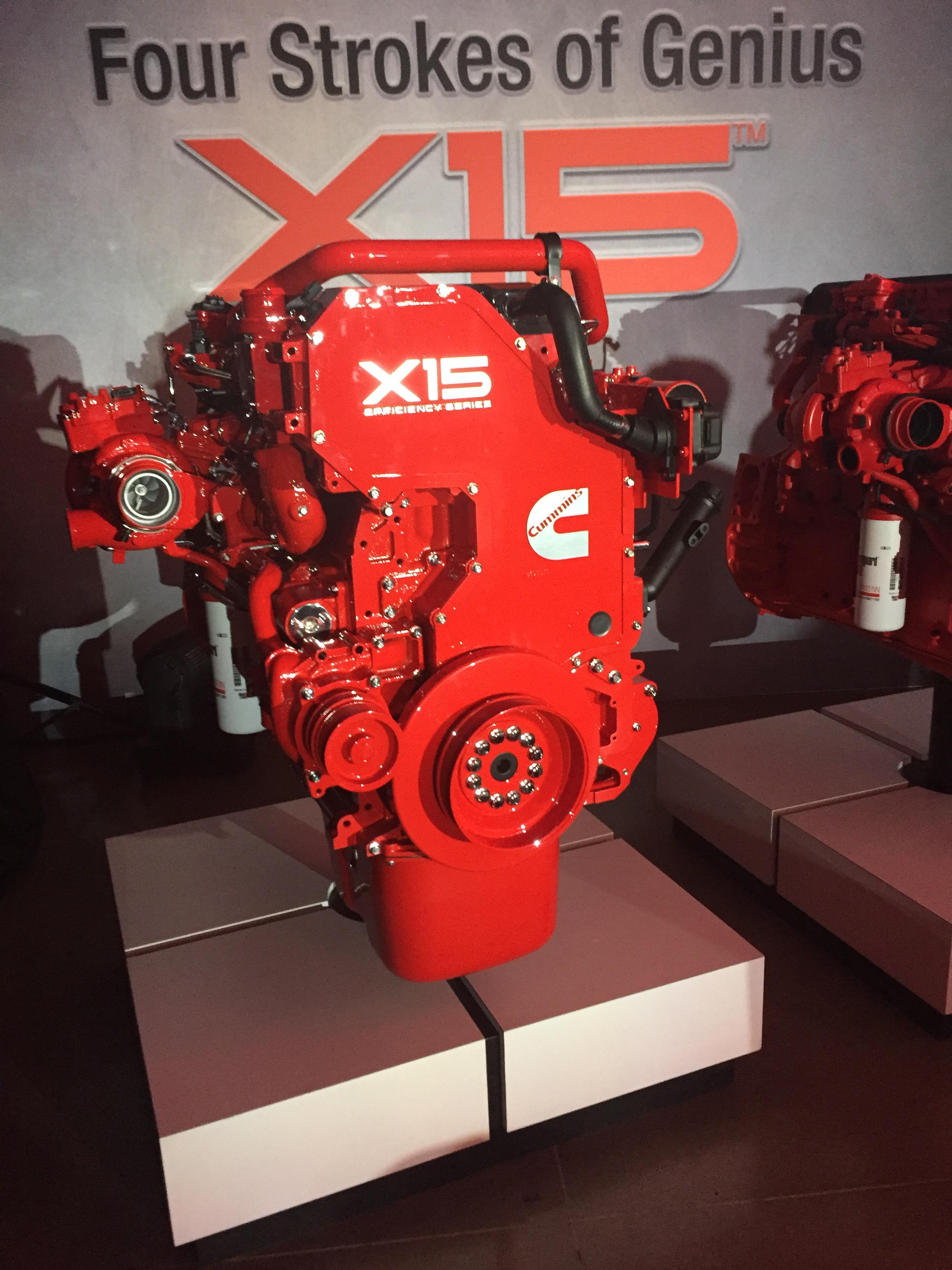
A simple solution to viewing the improvement opportunities is by using CMMS software. This is usually the case for small businesses scaling up their operations while still using traditional production processes. It can be very difficult to improve production efficiency if your company is not aware of their waste to begin with. Production Efficiency Improvement Example Note: For easier calculations, standard output rates are usually in the form of amount of work per unit time (e.g., square meters painted per hour). Standard output rate = 100 square meters / 30 hours = 3.33 square meters/hour If the standard rate of completing 100 square meters is 30 hours, and the worker you have hired took 34 hours to complete the job, production efficiency can be calculated as:Īctual output rate = 100 square meters / 34 hours = 2.94 square meters/hour Take this example of a job painting the walls of an office with a total painting area of 100 square meters. Production efficiency = (actual output rate / standard output rate) x 100% This value can be measured using historical data or through a time study process.Īs an equation, production efficiency can be expressed as: In this calculation, the standard output rate is defined as the amount of work that can be done per unit of time. In the case of measuring the productive efficiency of a worker, for example, an employee’s completion rate is compared to the baseline standard. Production efficiency is calculated by comparing the actual output rate to a standard output rate. Production efficiency, in most cases, is a more useful guideline for facility managers to ensure that costs are optimized, without sacrificing the quality of products. However, this can become problematic when the priority of the facility becomes too focused on purely reducing costs. Manufacturing facilities recognize the importance of being cost-effective.
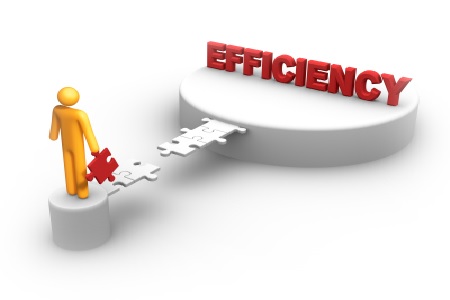
This allows companies to achieve a good balance between minimization of costs and maximization of resources, while maintaining a good quality of products. Instead of just measuring productivity levels, production efficiency also considers the amount of resources required for production. Looking at production efficiency usually happens when a system can no longer produce more goods without sacrificing the production of another related product.
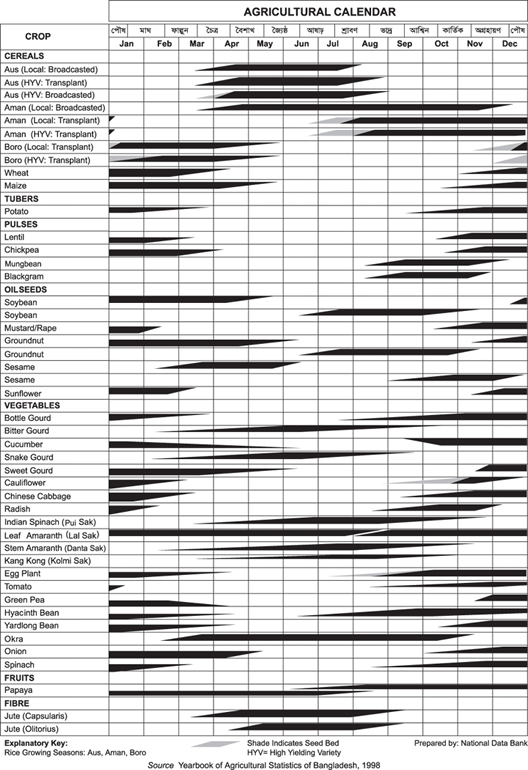
Basically, production efficiency looks at the maximum output you can achieve using the same assets that you already have. In order to achieve production efficiency, one should utilize resources and minimize waste, which in turn, translates to higher revenues. Production efficiency, also known as productive efficiency, identifies the conditions in which goods can be produced at the lowest possible unit cost.
